Elliott Turbomachinery
Companies around the world choose Elliott Group to design, manufacture and service their critical turbomachinery. Elliott turbomachinery operates in every imaginable application requiring rotating equipment, including oil & gas production and processing, refineries, chemical processing plants, steel mills, electricity generating stations, sugar mills, paper mills, plant oil processing plants, and municipal steam and waste facilities.
Our core products are centrifugal and axial compressors, steam turbines, cryogenic pumps & expanders, power recovery expanders, and related auxiliary equipment.
Elliott equipment is precisely engineered to meet our customers’ specific requirements. Around the world, customers turn to Elliott for precision engineering, extraordinary reliability and unparalleled service.
COMPRESSORS
COMPRESSORS
With thousands of compressors in service around the world, Elliott is a leader in gas compression, delivering state-of-the-art performance in a diverse range of industries including petroleum refining, petrochemical processing, cryogenic refrigeration (LNG), oil and gas production, gas compression and other industrial processes.
Elliott’s position on the cutting edge of compressor technology includes a number of engineering firsts. We pioneered refrigeration compression, high-pressure casing technology, the development of fabricated casings and improved impeller welding techniques. Elliott was among the first to utilize magnetic bearings in critical service centrifugal compressors.
Today Elliott compressors incorporate proprietary EDGE technology with advances in aerodynamics, rotor dynamics, computerized equipment selection, process simulation, and metallurgy. We understand that change is essential in achieving and maintaining a competitive edge, and together with our customers and suppliers,we continue to innovate, improve and expand our extensive portfolio of products and services.
Elliott’s full line of centrifugal and axial compressors are available in a wide range of configurations to meet mechanical considerations and process demands.
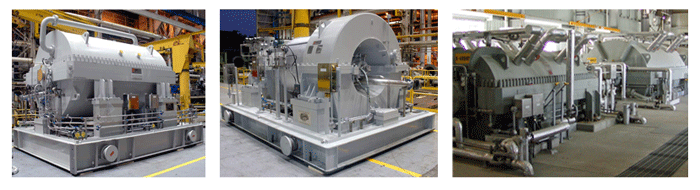
STEAM TURBINES
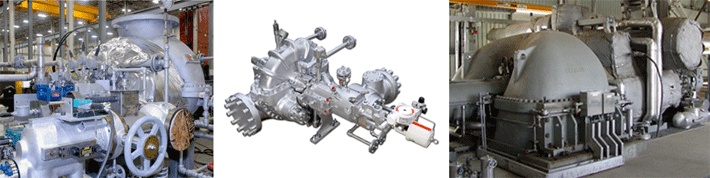
For nearly a century, Elliott steam turbines have earned a reputation as the most rugged, reliable, and versatile drivers in the industry. Combining engineering expertise, rugged designs, and precision manufacturing, Elliott steam turbines are built to perform and endure years of continuous service. These powerful workhorses provide exceptional value and performance in a broad range of mechanical and power generation applications, around the clock and around the globe, in environments of every extreme. With power requirements, steam conditions, and speeds constantly rising, Elliott has continued to develop its steam turbine product lines to meet ever more challenging operating conditions. Elliott steam turbines are rated for inlet steam conditions up to 2000 psig/1005 degrees F and speeds up to 20,000 rpm.
Elliott steam turbines come in a variety of sizes ranging from small, 20 HP (15 kW) single-stage units, to large 175,000 HP (130,000 kW) multi-valve, multi-stage extraction condensing units. These units can be built to API standards and can be customized to meet exacting customer specifications. With a large selection of both standard and engineered steam turbines and turbine generator sets, Elliott steam turbines boost production in industries as diverse as oil and gas, chemical and petrochemical, pulp and paper, power generation and food processing. Whatever the application requires, the world can turn to Elliott for a steam turbine solution.
CRODYNAMIC PRODUCTS
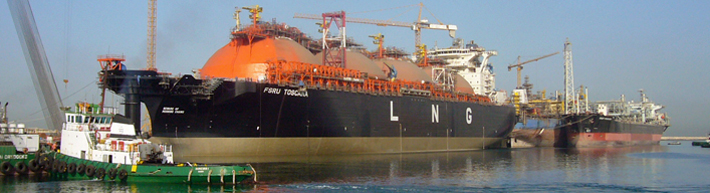
Continuous Advances in Cryogenic Technology for Liquefied Gas Applications
For over 40 years, Cryodynamic Products has been the premier manufacturer of both standard and custom cryogenic pumps and expanders, delivering continuous advances in equipment design and technology to customers around the world. With thousands of installations worldwide, Elliott’s Cryodynamics® business is the recognized global leader for submerged electric pumps and expanders in liquefied gas applications.
Cryodynamic Products provides onshore and offshore solutions for liquefaction, storage, and regasification for liquefied gas carriers, FSRU, FLNG, FSU, LNG bunkering, and LNG fueling applications. We developed the first submerged cryogenic expander in 1997, the first two-phase expander in 2001, the first two-phase tandem installation in 2008, and the first floating application in 2011.
In addition to our full line of submerged cryogenic pumps and expanders, we offer complete global service packages including parts, service engineering, training, and customized research.
Our new state-of-the-art cryogenic testing facility, which was dedicated in October 2021, is like no other cryogenic testing facility anywhere in the world. Learn more about it and how it is contributing to Elliott’s sustainability objectives.
STEAM TURBINE GENERATOS
Intelligent Alternative for Power Generation
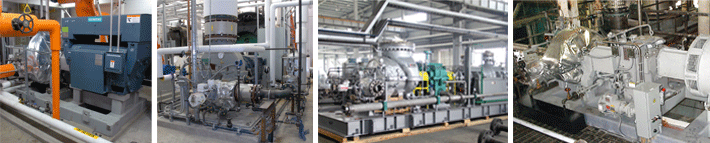
Elliott steam turbine generators (STGs) offer an intelligent alternative for reliable, efficient and cost-effective on-site power generation. Our custom-designed STG sets support commercial energy requirements for continuous or standby power up to 50MW, including renewable energy applications and green energy initiatives. Elliott’s steam turbine designs incorporate industry standards such as API 611 and API 612, and National Electrical Manufacturers Association (NEMA) specifications SM-23 & SM-24 when required for all new units, aftermarket conversions, and re-rates.
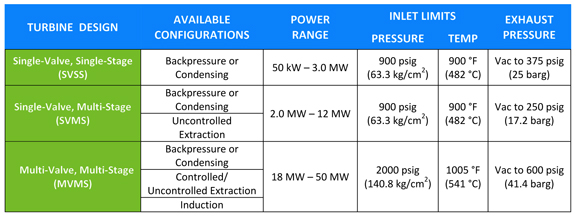
POWER RECOVERY EXPANDERS
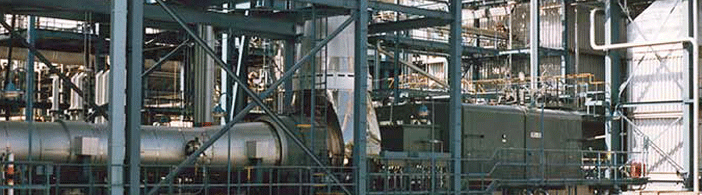
Elliott power recovery expanders are the most dependable and durable designs in the industry. Elliott pioneered power recovery expander turbine technology in the 1950s and has been a leader in the field ever since. An Elliott TH power recovery expander turbine converts high temperature, low pressure flue gas energy into usable power. The turbine often is used to drive compressors or generators in refinery fluid catalytic cracking (FCC) service. Recovery power for these applications can approach 50,000 hp (37,300 kW).
Elliott design engineers continue to advance expander technology to meet the changing demands of the FCC process. By using computational fluid dynamics to verify flow path design and minimize blade erosion, we have significantly extended typical time between turnarounds far beyond the industry average, without sacrificing efficiency. To ensure reliability, we design all critical components using finite element analysis. We are continuously developing new coatings and materials to resist the erosive and corrosive environment of the FCC process.